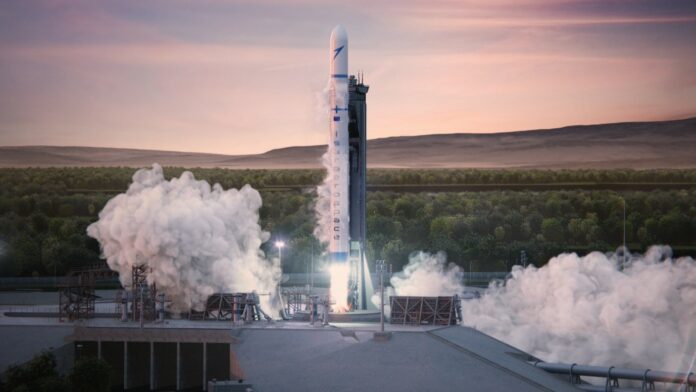
With 1000’s of layer pictures to research when looking for errors, it’s straightforward to overlook a important defect that can outcome within the non-validation of an element. The actual fact is the powder recoating carried out after every printed layer is vulnerable to error: If the floor to be uncovered just isn’t coated evenly and utterly, this may result in defects within the element.
To handle this answer, AM customers more and more flip to automated software program options that would assist them do the job throughout the 3D printing course of. It’s the case of aerospace firm Isar Aerospace that not too long ago built-in the nebumind software program into its 3D printing course of (LPBF – Laser Powder Mattress Fusion) to automate the identification and reporting of defects throughout the software of a brand new powder layer.
The corporate of the identical title is predicated in Germany and develops analytics software program shops and visualizes manufacturing knowledge as digital product twins. Its software program detects defects by automated evaluation of the powder mattress pictures, offering the engineer with vital data for evaluating the standard of the printing course of.
The issue with the handbook evaluation of recoater pictures
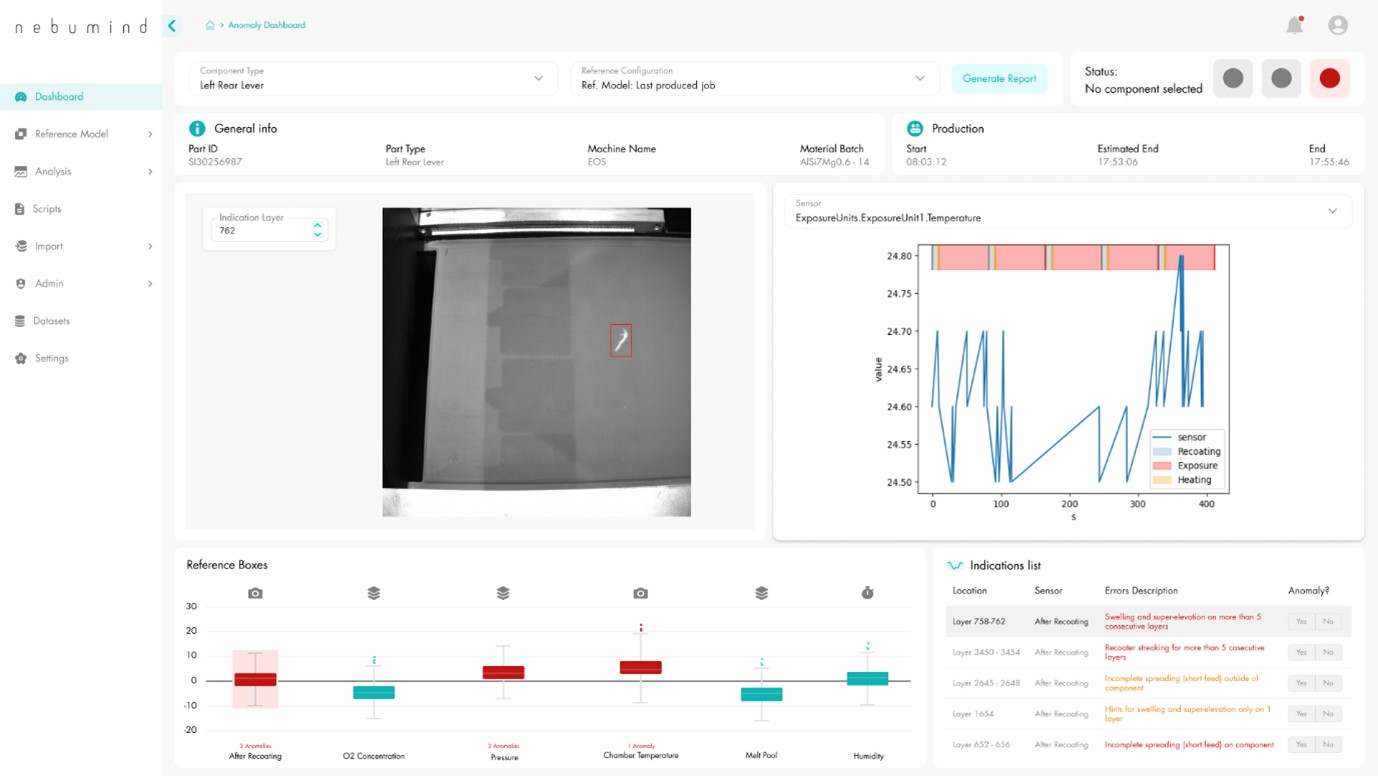
The issue is straightforward: sensors and cameras built-in into the L-PBF programs monitor the coating step, which might be manually analyzed for uncoated areas, injury to the recoater or different defects by engineers chargeable for the method. This method is extraordinarily time-consuming: as an illustration, if a 3D printed steel element generates 2,500 recoater pictures and an engineer takes 3 seconds to research every picture, they spend greater than 2 hours on this process for one construct job alone. Furthermore, because the evaluation is carried out in a post-processing step, defects are normally solely recognized after a element has been printed.
nebumind automates picture evaluation and presents defects in-process in digital twin format
To stop this handbook course of, Isar Aerospace has related the nebumind software program into its machine setting automating the defect detection for every recoating layer. The software program receives powder mattress pictures earlier than and after recoating, generated by an optical digital camera with a decision of 1280×1024 pixels, and extracts them robotically by way of the direct machine interface. The software program makes use of an algorithm to identify defects within the pictures robotically. For its algorithm, nebumind has employed primarily steady algorithms from picture and edge detection. As well as, the positions of the defects are analyzed throughout a number of layers to attenuate the false optimistic fee.
Based on nebumind, Isar Aerospace has been in a position to save as much as 80% utilizing its software program in comparison with the earlier handbook evaluation, as engineers can deal with the photographs labeled by the algorithm.
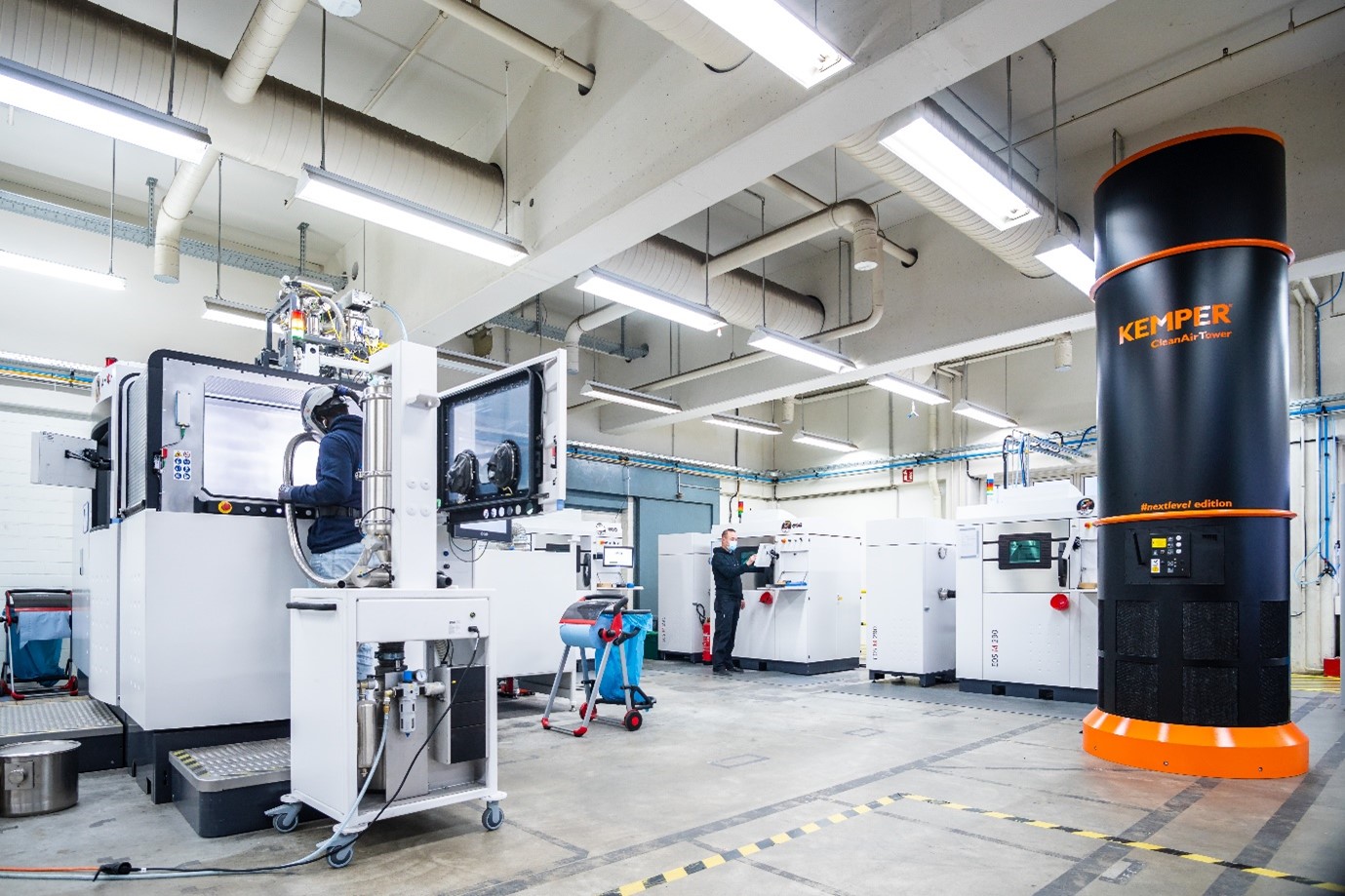
Learn extra in regards to the identification of defects throughout the steel 3D printing course of.
Shifting ahead, nebumind’s defect recognition will probably be moved upstream from post- printing to in-process, in order that the software program will be capable to level out doable anomalies instantly after coating, thereby enabling the consumer to cease the printing course of within the occasion of an irreparable defect. To additional automate the method, it’s deliberate to correlate the discovered recoater defects with different course of knowledge from the print job and CT knowledge from the ultimate high quality verify to determine root causes and forestall recoater defects from occurring within the first place. In the long run, nebumind not solely needs to watch the printing course of with its software program, but in addition to intervene within the course of in a regulating method, for instance to cease the printing course of within the occasion of irreparable errors or to compensate for an incorrect coating within the subsequent layer, the corporate explains.
Keep in mind, you may submit job alternatives within the AM Business on 3D ADEPT Media free of charge or search for a job by way of our job board. Be sure that to comply with us on our social networks and subscribe to our weekly publication: Fb, Twitter, LinkedIn & Instagram ! If you wish to be featured within the subsequent difficulty of our digital journal or for those who hear a narrative that must be heard, ensure you ship it to [email protected]