Researchers on the US Division of Vitality (DoE)’s Oak Ridge Nationwide Laboratory (ORNL) have 3D printed defect-free tungsten elements with complicated geometries.
Produced utilizing electron-beam additive manufacturing on the ORNL’s Manufacturing Demonstration Facility (MDF), these tungsten elements are stated to be the primary of their type. In accordance with the ORNL crew, this accomplishment provides important potential for clear power applied sciences, equivalent to fusion power.
The 3D printed elements have been designed for excessive environments, with tungsten possessing the very best melting level of any steel. As such, the fabric is properly suited to make use of in fusion reactors, the place plasma can attain temperatures above 180 million levels Fahrenheit. That is considerably hotter than the solar’s centre, which is available in at 27 million levels Fahrenheit.
“Electron-beam additive manufacturing is promising for the processing of complicated tungsten geometries,” commented Michael Kirka, Group Chief of the Deposition Science and Expertise Group at ORNL.
“This is a vital step for increasing using temperature-resistant metals in power sources that may help a sustainable, carbon-free future.”
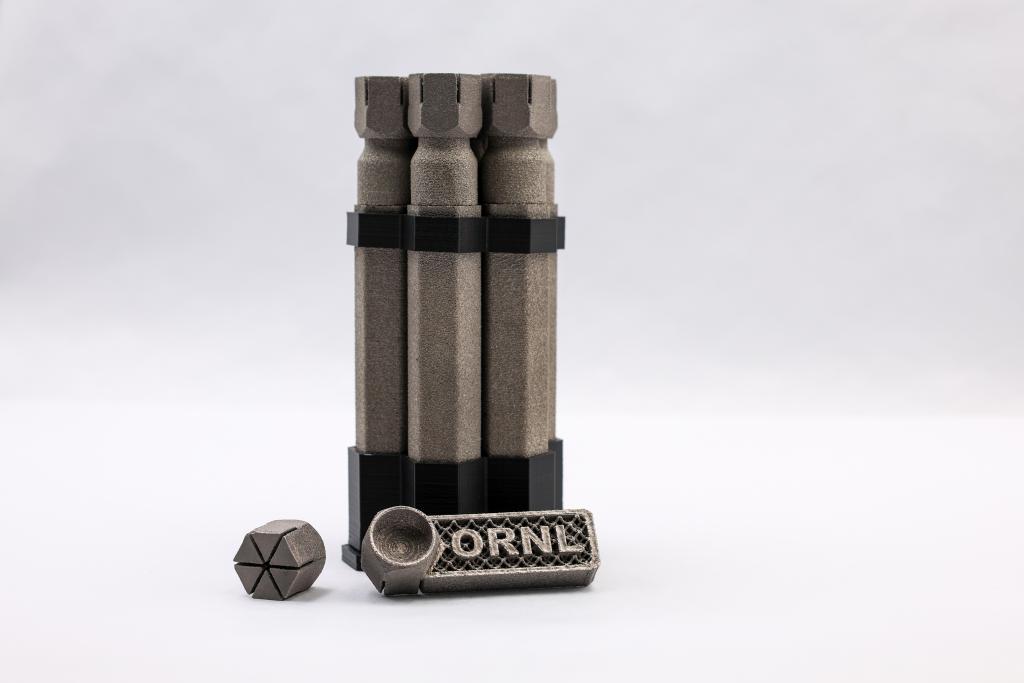
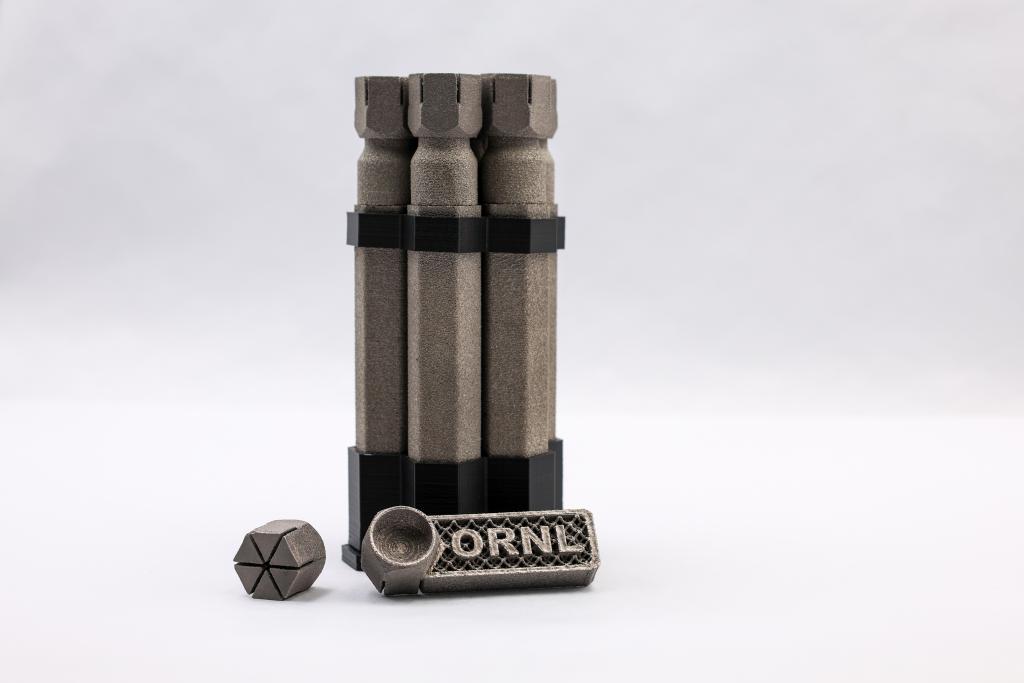
3D printing defect-free tungsten elements with complicated geometries
Regardless of its potential to resist excessive temperatures, manufacturing complicated tungsten elements is a difficult course of. Considerably, when in its pure kind, tungsten is brittle and may simply shatter at room temperature.
To beat this, the ORNL crew developed an electron-beam 3D printer, which might deposit tungsten layer by layer into exact and complicated 3D geometries.
The system employs a magnetically directed stream of particles in a vacuum to soften and bind tungsten powder into solid-metal objects. Because of its high-vacuum enclosure, the electron beam 3D printer reduces contamination from international supplies and limits residual stress formation.
This analysis kinds a part of the DOE’s efforts to advance clear power by the event of latest renewable sources, equivalent to nuclear fusion. The ORNL has beforehand used additive manufacturing to reinforce know-how for established nuclear power functions.
In 2020, it was introduced that ORNL had 3D printed gasoline meeting brackets for the Tennessee Valley Authority’s (TVA) Browns Ferry Nuclear Plant in Alabama. The elements have been developed in partnership with nuclear gasoline provider Framatome as a part of the Transformational Problem Reactor (TCR) Program primarily based at ORNL. This initiative explores alternatives for quicker and cheaper nuclear power distribution throughout the US.
The TCR Program has additionally seen ORNL develop a 3D printed nuclear reactor core. By means of this undertaking, ORNL sought to determine new strategies in reactor design, manufacturing, licensing and operation.
In 2020 the crew offered its design for the reactor core, scaled up the additive manufacturing know-how obligatory to construct it, and developed strategies to substantiate the consistency and reliability of the 3D printed elements.


3D printing bolsters renewable power sector
Additive manufacturing is witnessing rising adoption to help world efforts to transition away from conventional non-renewable power sources and undertake greener alternate options.
Beforehand, GE’s wind turbine manufacturing division, GE Renewable Vitality, invested in construction-3D printing specialist COBOD to assist drive this renewable power transition. This funding expanded on earlier collaborative efforts between the 2 firms, which has seen them work to co-develop 3D printed “report tall” wind turbine towers.
Elsewhere, researchers on the U.S. Nationwide Renewable Vitality Laboratory (NREL) developed a novel course of for 3D printing wind turbine blades utilizing recycled resin. Stated to enhance the efficiency and end-life recyclability of the blades, the 3D printing course of makes use of thermoplastics that may be melted and reused.
To display the effectiveness of this method, the engineers fabricated a 13-meter prototype. The crew believes that this course of might yield value and pace positive factors for producers. The researchers famous that 3D printing might cut back the load and price of turbine blades by 10%, and lower lead instances by 15%.
Wish to assist choose the winners of the 2024 3D Printing Business Awards? Be a part of the Knowledgeable Committee immediately.
What does the way forward for 3D printing maintain?
What near-term 3D printing developments have been highlighted by business consultants?
Subscribe to the 3D Printing Business publication to maintain updated with the newest 3D printing information.
You may also comply with us on Twitter, like our Fb web page, and subscribe to the 3D Printing Business Youtube channel to entry extra unique content material.
Featured picture exhibits the 3D printed complicated, defect-free tungsten elements. Picture by way of Michaela Bluedorn/ORNL, US DoE.