The rapidly-increasing commercialization within the 3D printing area has already led to huge progress in particular verticals like ceramics and steel. A current report urged that the ceramic 3D printing market might attain 384 million USD by 2025. The steel market, which is taken into account one of many quickest rising within the AM sector, is predicted to surpass $18B by 2032 for comprehensible causes.
3D printing utilizing the above supplies allows the creation of advanced components with superior mechanical properties. NanoParticle Jetting™, the signature strategy of AM 3D printing chief XJet, is suitable with each ceramics and metals, providing an automatic, secure, environmentally pleasant path towards scale manufacturing of high-quality, geometrically advanced components. We spoke with the corporate’s CMO, Man Zimmerman, to study extra concerning the expertise, its advantages, and XJet’s distinctive strategy.
3DN: May you introduce your self and Xjet?
My title is Man Zimmerman. I joined Xjet just lately because the CMO as the corporate gears up for progress. I’ve numerous expertise, although most related is my background in international enterprise. In the meantime, Xjet is a 3D printer producer that’s addressing essentially the most difficult phase in additive manufacturing, metals and ceramics. Top quality, prepared to make use of steel and ceramic components that go into manufacturing and never into prototyping: that’s the ambition utilizing our personal patented NanoParticle Jetting™ (NPJ) expertise.
In the meantime, Xjet is a 3D printer producer that’s addressing essentially the most difficult phase in additive manufacturing, metals and ceramics. Top quality, prepared to make use of steel and ceramic components that goes into manufacturing and never into prototyping, that’s the ambition utilizing our personal patented NanoParticle Jetting™(NPJ) expertise.
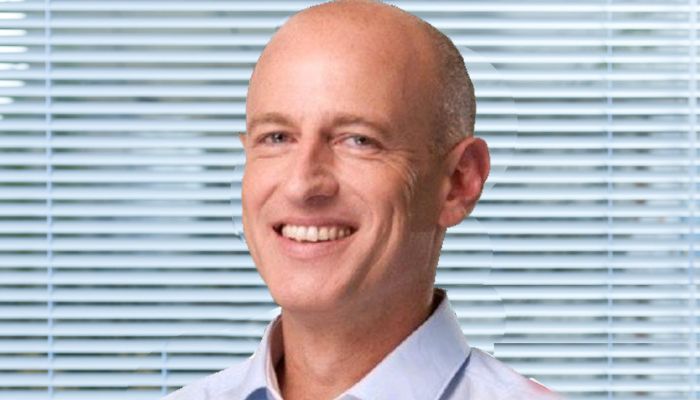
Man Zimmerman
3DN: How does NPJ work? What are the advantages of utilizing it?
NPJ delivers clear, automated manufacturing of top of the range components in steel and ceramics with out involving powders, handbook labor, or put up processing . What allows this breakthrough is XJet’s distinctive additive manufacturing course of primarily based on nano-particles direct materials jetting, which print high-resolution components utilizing the hardest supplies in scale. On this course of, the assist supplies and the principle supplies are each inks, not powders, a revolutionary strategy in AM.
Let’s dive somewhat deeper into the printing process. We name it: Print-Wash-Sinter. The fundamental precept is utilizing procurable materials primarily based on nanoparticles. With this, we’re capable of concurrently print the fabric and the assist, which is a really arduous however soluble materials. As soon as we full the construct, the assist is washed away in water through an automated course of. The ultimate sintering section is finished in a normal business furnace, however in a considerably decrease temperature than powder primarily based options. This allows the very best complexity, accuracy and a degree floor. It additionally removes design-related constraints. The expertise and using skinny nanoparticle layers and soluble assist allow the creation of advanced, correct geometries, together with inside parts. This additionally permits for brand spanking new design capabilities in a means that was thought of unattainable up till now.
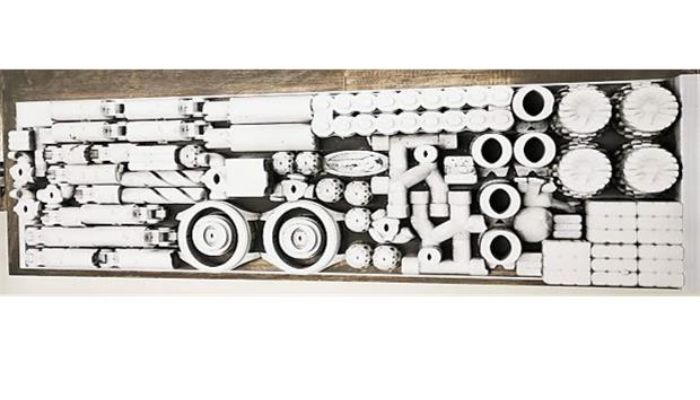
Xjet is able to making a variety of fantastic options
The result’s high-quality, extremely correct components straight off the method. The printed components don’t require any further processing or machining. Similar to the XJet slogan, all you’ll want to do is print, wash, and sinter.
One other benefit introduced by nanoparticles has to do with the power to print remarkably skinny layers. The density degree is considerably larger in comparison with different additive applied sciences, reaching highest ranges of fabric purity, density and floor smoothness. This considerably improves the components’ efficiency and reduces the sintering impact.
As it’s possible you’ll know, the sintering course of turns the particles into the precise materials, which frequently ends in vital shrinkage. With XJet’s expertise, the method is finished at a temperature decrease than 200C, which saves time, boosts density, and reduces isotropic and general shrinkage. Shrinkage stays the identical alongside the x, y and z axes, leading to no distortions within the ultimate half. This proprietary and groundbreaking expertise is packed in a excessive throughput manufacturing system. It’s a digital, automated course of as an alternative of a handbook, unsafe, polluting course of that ends in lower-quality components.
3DN: What are the functions for Xjet’s options?
Along with our market main prospects we’re focusing on particular verticals and functions in all three business domains: Industrial, Medical, and Client items.
In relation to ceramics, principally Alumina and Zirconia, which supply very excessive resistance to warmth, corrosion and electrical isolation, the liberty of design we convey to this market opens up alternatives in industrial functions (e.g. semiconductors manufacturing tools components, warmth exchangers and electrical energy connectors, wave-guard antennas and electrical board components).
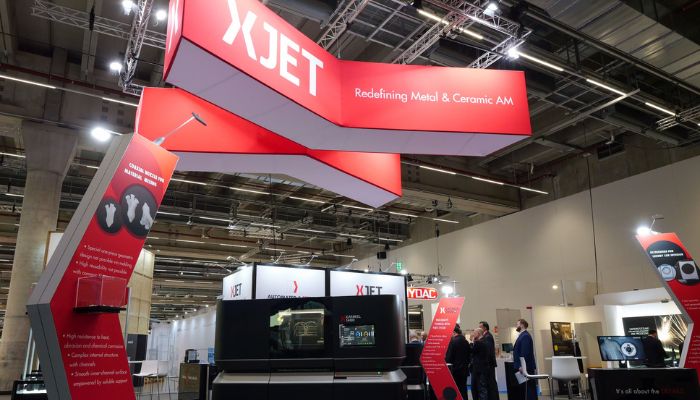
Xjet had been current at Formnext 2022
Dental implants and crowns are one other apparent vertical that we’re moving into which is without doubt one of the rising medical markets in the present day. In client items we deal with excessive worth wearables like high-end earbuds (which is an intriguing software, because the printed components are very small, nonconductive, and customised to supply prime acoustic qualities), and luxurious watches.
We even make a number of ceramic components in our excessive efficiency Carmel1400 system, so principally we print our personal components with our personal machines. Metallic is a newer expertise getting into the market changing conventional MIM (Metallic Injection Molding) for brief runs and excessive selection components like surgical gadgets, hydraulic programs components and lots of extra.
We assist a spectrum of distinctive functions that require a excessive amount of components, changing a number of conventional applied sciences. The checklist consists of MIM (steel injection Molding), CNC, and funding casting, a central expertise with small components that struggles every time half manufacturing is below 20,000, making our expertise a extra economical selection.
3DN: Why did Xjet resolve to launch a steel answer?
After we established the ceramics expertise amongst market leaders and ceramic technical leaders, we finalized the event of the steel a part of the portfolio with two main stainless-steel supplies. Metallic is a a lot bigger and diversified market. Growing the steel answer was more difficult, however we’ve reached unprecedented efficiency ranges, even higher than ceramics. In early 2022, we launched it to the market after going via a protracted analysis course of.
It’s now accessible, and we showcased it at Formnext 2022 with testimonials from the expertise’s main beta customers. Guests discovered how this steel answer competes with a number of powder-based applied sciences, providing clear benefits as an automatic, clear steel course of to be used in quite a lot of sectors.
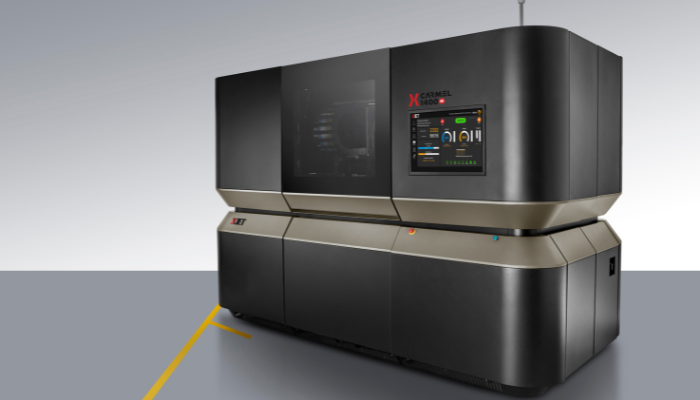
Xjet’s steel answer
The expertise provides a number of advantages. First, we had been capable of develop soluble assist supplies that may work with the steel, an enormous benefit for a lot of customers. One other is the high-quality floor degree of the half, which is obvious proper out of the machine with out demanding any further processes. The third profit is producing extremely advanced components with accuracy, a large benefit for a lot of functions.
Simply for instance this, we are able to print the wristband of a luxurious watch from stainless-steel as a complete. It would want somewhat little bit of sharpening, however that’s it. We’re capable of print so precisely that we are able to print the wristband bearings contained in the half, no have to assemble it. NJP offers customers the power to print extraordinarily correct, high-performance components in steel which can be ready-to-use because of the distinctive functionality of jet versus powder. We deal with customers who wish to create high-performance, correct components in varied consumer-facing verticals.
3DN: One other side you might be happy with is the sustainability of your course of. How precisely is it environmentally pleasant?
To start with, it’s secure. The supplies are secure, they arrive in closed bottles, and there aren’t any poisonous particles or free powder . It’s a secure course of for individuals who function it, which isn’t the case for a lot of AM and conventional processes. Moreover, it makes use of precisely the quantity of fabric wanted for the half. It doesn’t waste something in a really additive constructing course of.
Our assist materials is soluble in water and could be safely drained. It comprises some minerals, however is so secure it might go as ingesting water in some locations. That is safer for people but additionally the atmosphere, because it nearly eliminates waste disposal points.
Final however not least, our sintering can also be extra eco-friendly in comparison with many different processes. It’s usually essentially the most energy-consuming a part of the method, however as a result of we conduct it at comparatively low temperatures for a decrease interval, we save various power. These key elements make NJP some of the environmentally pleasant processes in steel and ceramics.
3DN: Any final phrases for our readers?
To summarize, NPJ expertise provides three main benefits. Nanoparticles in ink make it safer and extra correct, reaching larger density. The second profit is rooted within the constructing course of, printing the thinnest layers to attain unbeatable limitless complexities and true Design for Performance. And the third is the inexperienced aspect. Our components could be cleaned in water, leaving no residue.
The method itself consists of solely three steps: print, wash, and sinter. Shifting ahead, we consider the expertise will turn into a significant half within the digital transformation of ceramic and steel, industrial, high-quality, advanced components manufacturing. You possibly can study extra about XJet on our web site HERE or take a look at the video beneath to know how our expertise works.
What do you consider Xjet? Tell us in a remark beneath or on our LinkedIn, Fb, and Twitter pages! Don’t overlook to join our free weekly E-newsletter right here, the newest 3D printing information straight to your inbox! You can too discover all our movies on our YouTube channel.
*All Picture Credit: Xjet