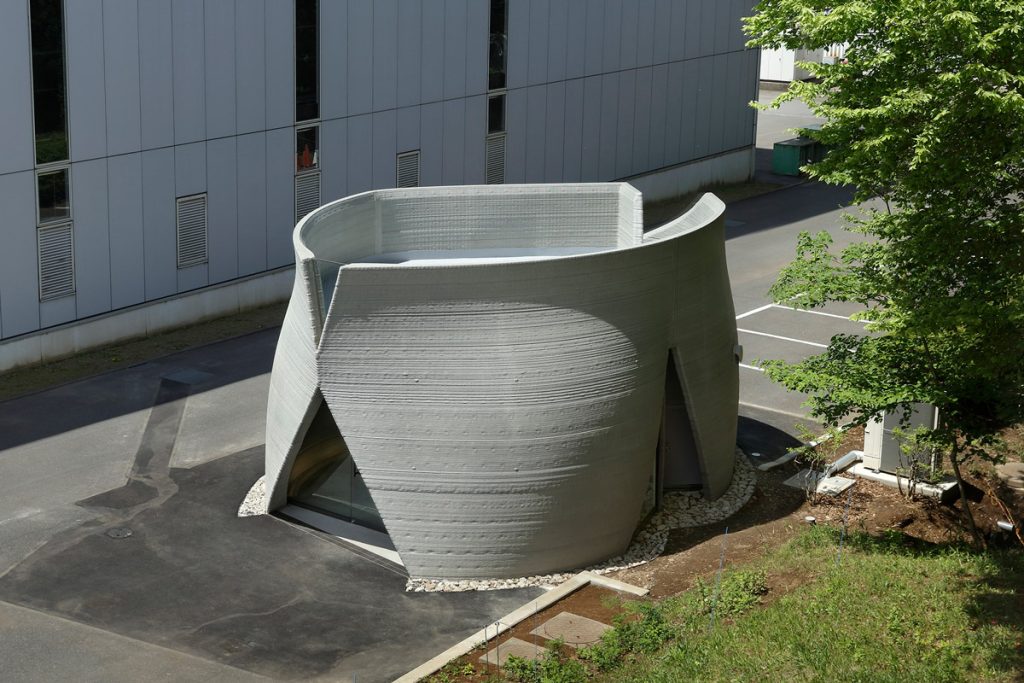
Obayashi, one of many largest common contractors in Japan, based in 1892, has accomplished “3dpod”, the primary 3D-printed and earthquake-proof constructing within the nation to obtain ministerial certification and a constructing allow. The demonstration facility, open to the general public, was constructed to judge the sturdiness, structural, and environmental efficiency of 3d-printing, and to foster additional its technological growth.
Architectural 3D printing is especially difficult in earthquake-prone Japan, and, resulting from constructing regulation restrictions, it has thus far been employed solely in civil engineering and non-habitable, small buildings. The primary aim of the undertaking was to fulfill the strict native necessities with out counting on standard reinforcement.
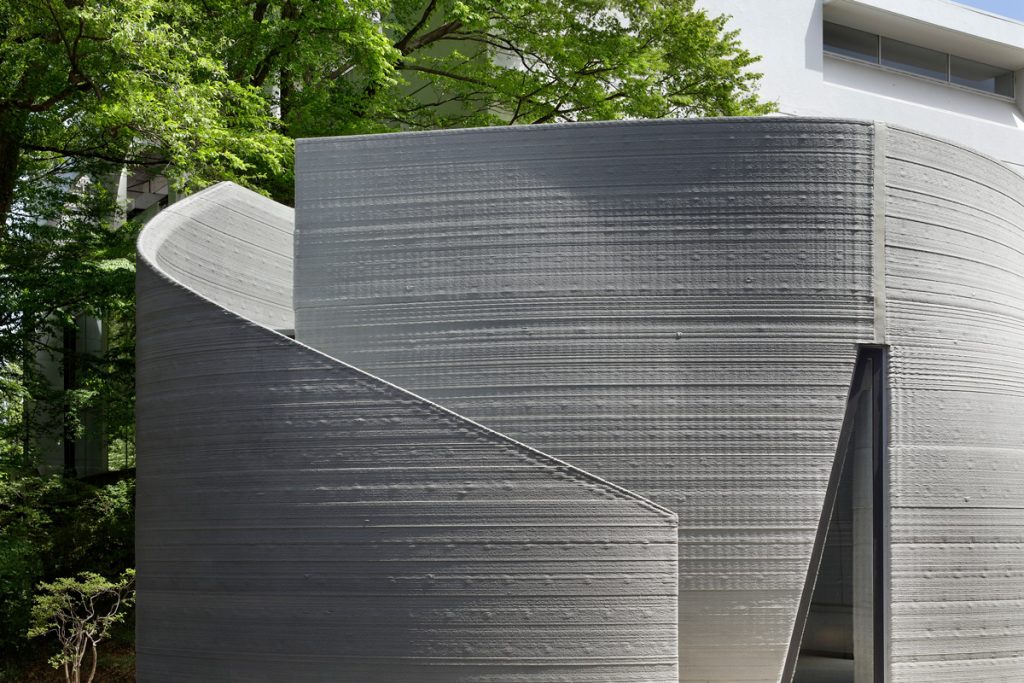
3dpod is printed with a particular mortar, performing each as an inner and exterior ending floor in addition to the framework for the load-bearing construction, product of a high-strength concrete bolstered with metal fibers, referred to as “SLIM-Crete®”. This building methodology doesn’t require the location of reinforcing bars nor metal frames, to not restrict the aesthetic potential of 3D printing.
The pod-like form is derived by maximizing the ratio between inside house and wall-surface space, i.e., attaining the biggest inner quantity with the least quantity of fabric, given the technical printing constraints and the restrictions of the positioning.
The partitions are multi-layered, combining load-bearing construction and cavities for insulating materials, tools routing, and a system for radiant heating and cooling, to afford the extent of habitability of a traditional constructing. Building time could be lowered by designing and printing these programs directly, with the ability to perform completely different building duties concurrently.
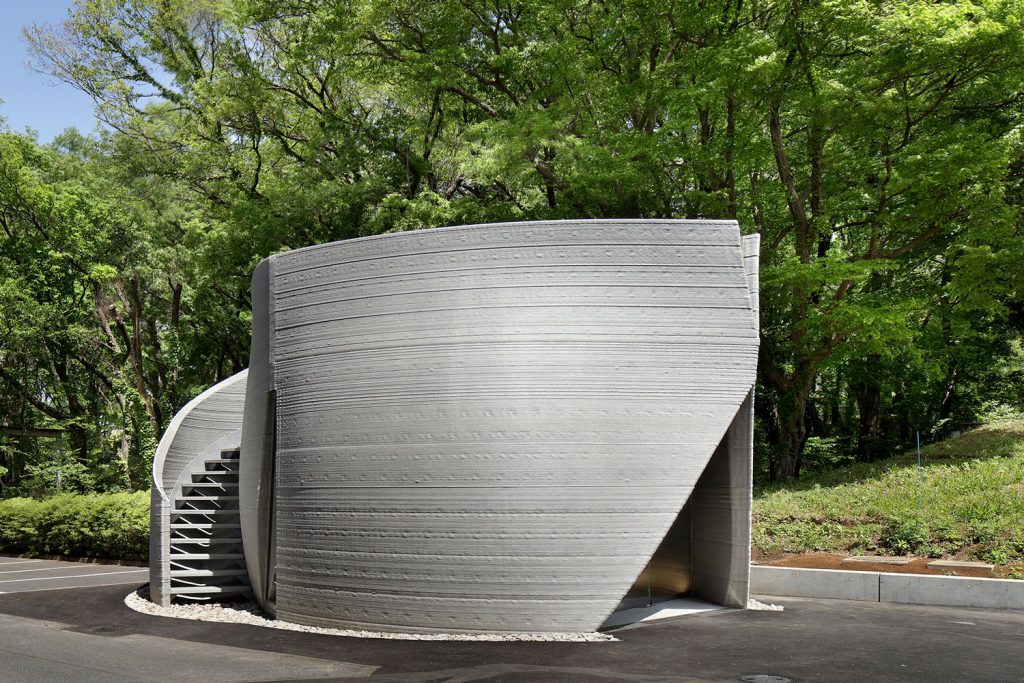
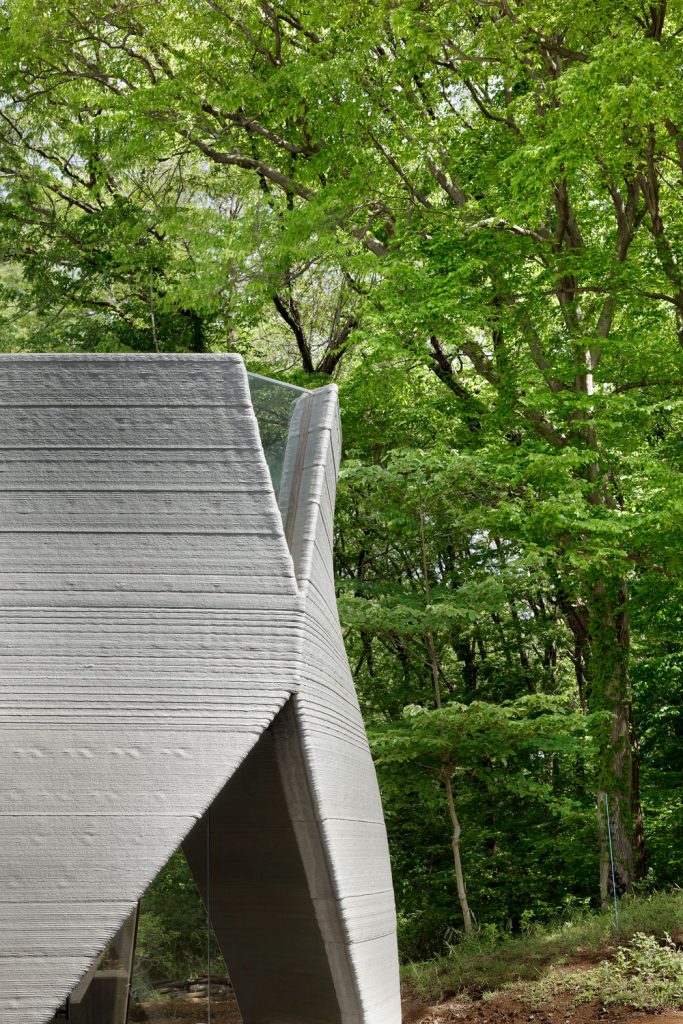
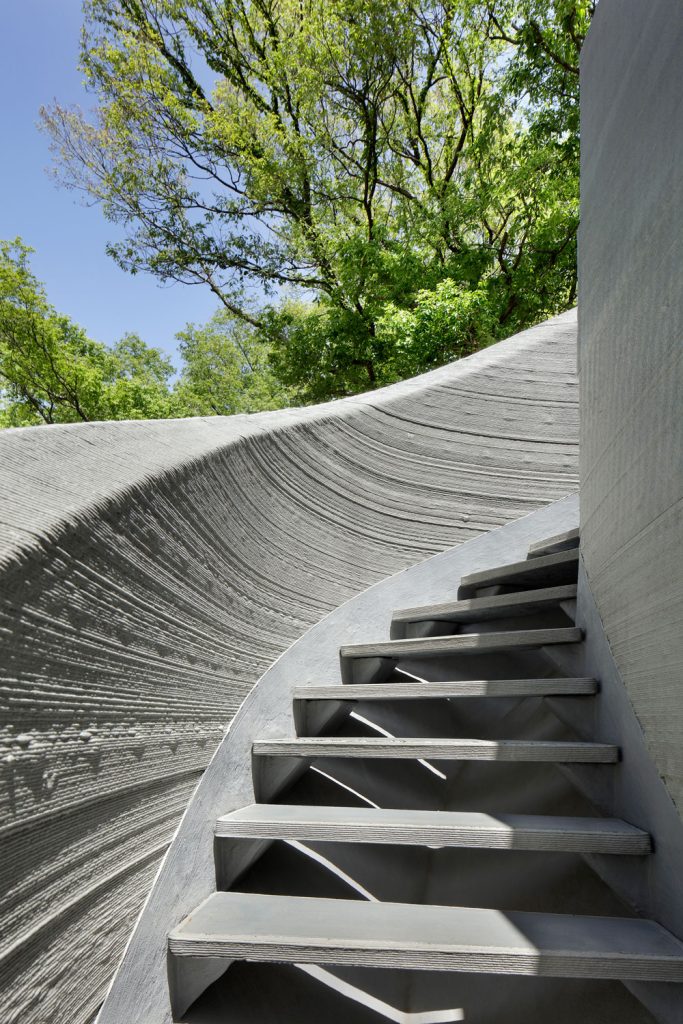
The slab design options strengthening ribs following principal stress strains, a method of fabric economic system attaining aesthetic and spatial qualities on the similar time: This consequence would have been unfeasible utilizing standard building strategies.
To manufacture 3dpod, a robotic printer was put in on-site, printing the mortar formwork instantly onto the foundations. The roof-slab formwork was as a substitute printed as a precast component at a close-by facility, then positioned on high of the partitions and capped with SLIM-Crete®, making a shell construction. Thereafter, the 3D printer was positioned on the roof slab to complete off the parapet of the walkable deck, demonstrating the technical feasibility of a multi-storied printed constructing.
Regardless that 3dpod is the results of cutting-edge digital fabrication, it retains a sure heat and haptic enchantment. That is because of the distinctive texture rising from on-site building strategies, that are harking back to craftsmen’s handiwork and grant the constructing an interesting roughness and primitive aura.
Architectural 3D printing can scale back labor demand on the development website, shorten building time by means of automation, and save on CO2 emissions, due to lowered transportation of constructing supplies. At Obayashi, we are going to proceed to advance the event of 3D printing within the AEC business, concentrating on the persistent scarcity of expert employees and building points in distant areas, all of the whereas selling the diversification of constructing supplies, and aiming for a localized building course of.
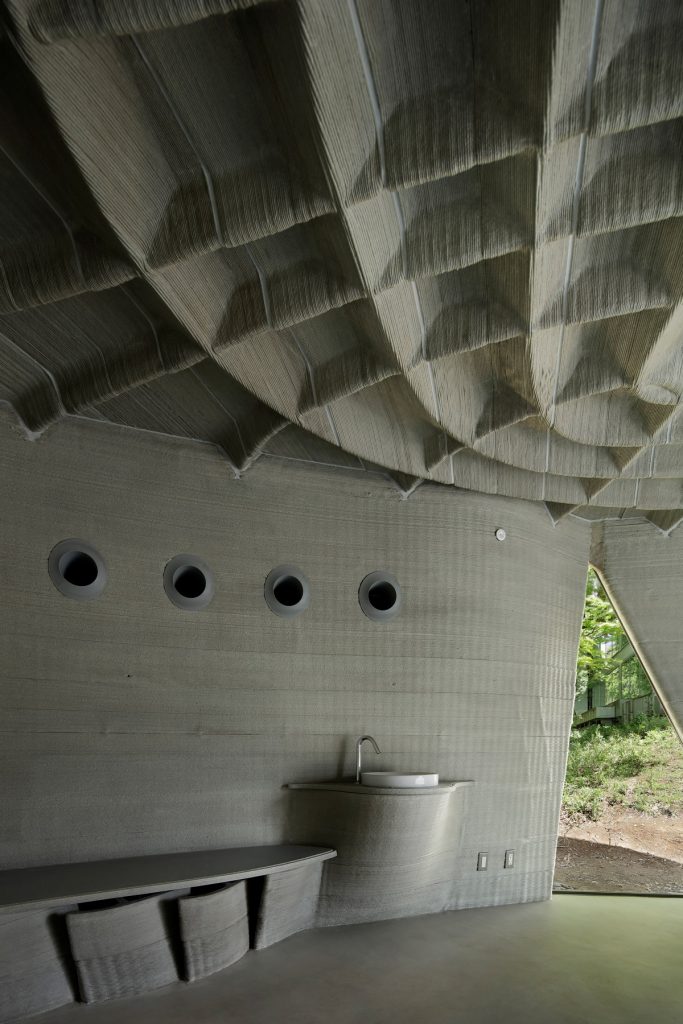
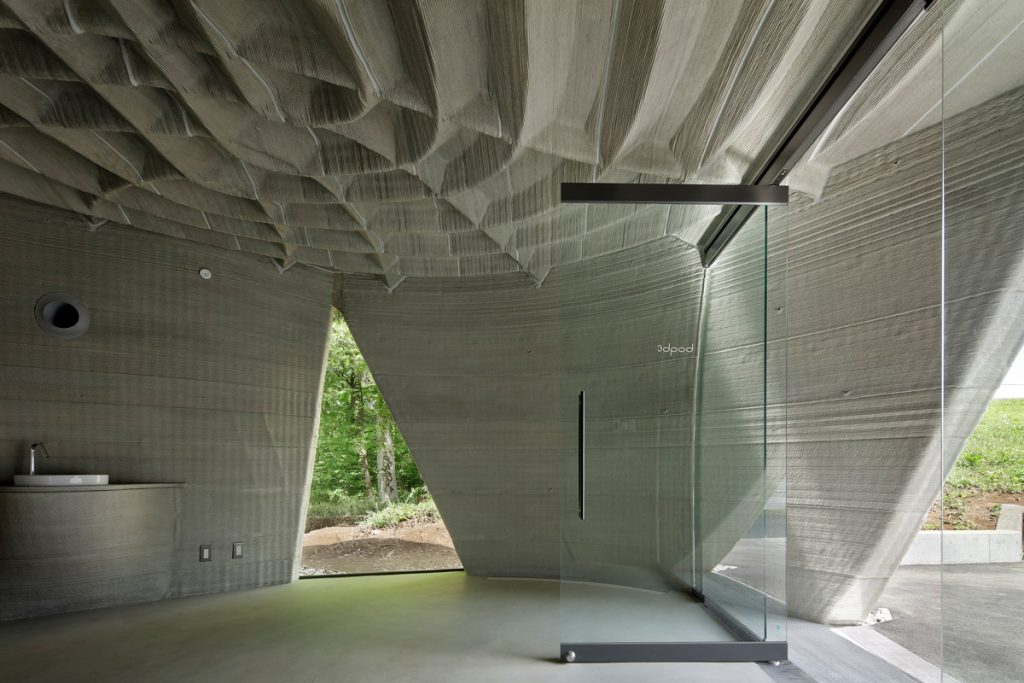
Challenge Information
Challenge Identify: 3dpod
Challenge Location: Kiyose (Tokyo), Japan
Structure Agency: Obayashi
Architect: Obayashi Company Architects and Engineers
Metropolis: Tokyo
Nation: Japan
Photographer: Satoshi Shigeta and Obayashi
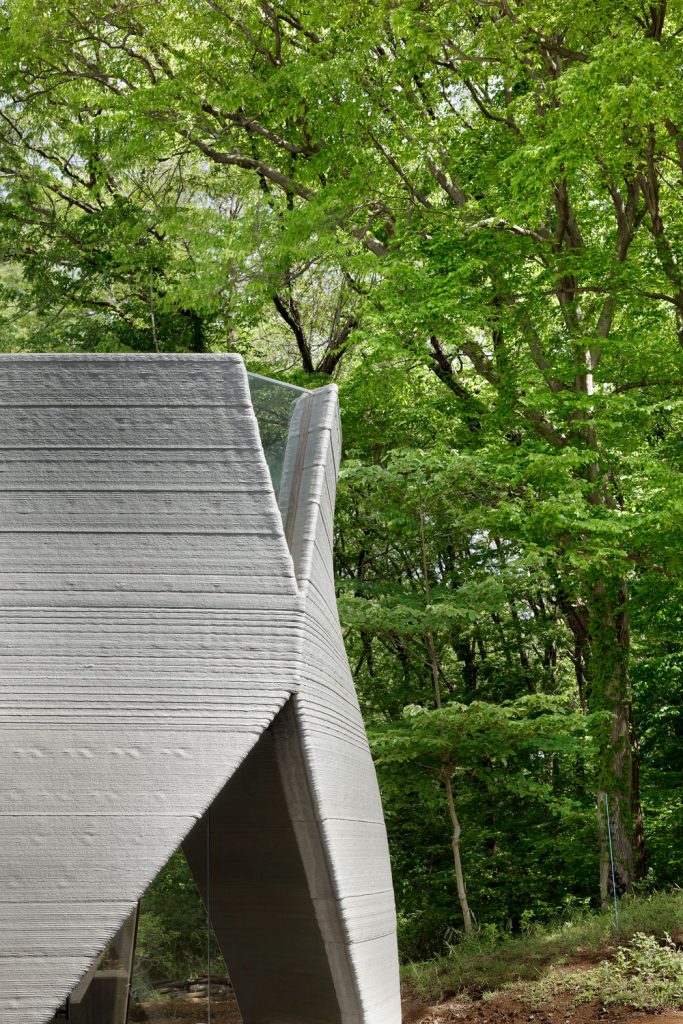
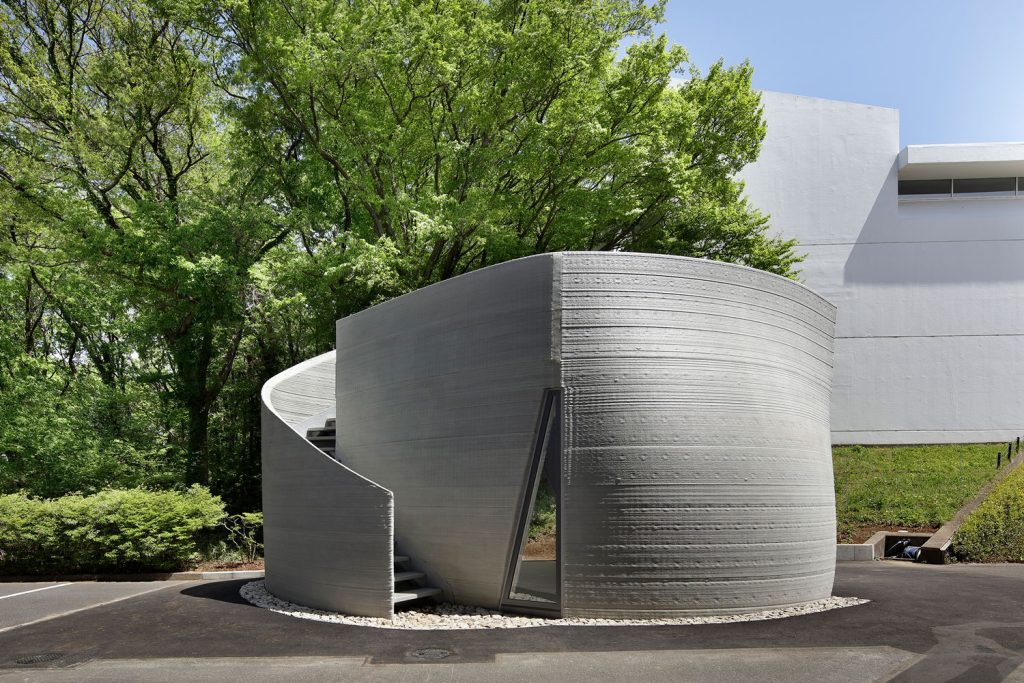
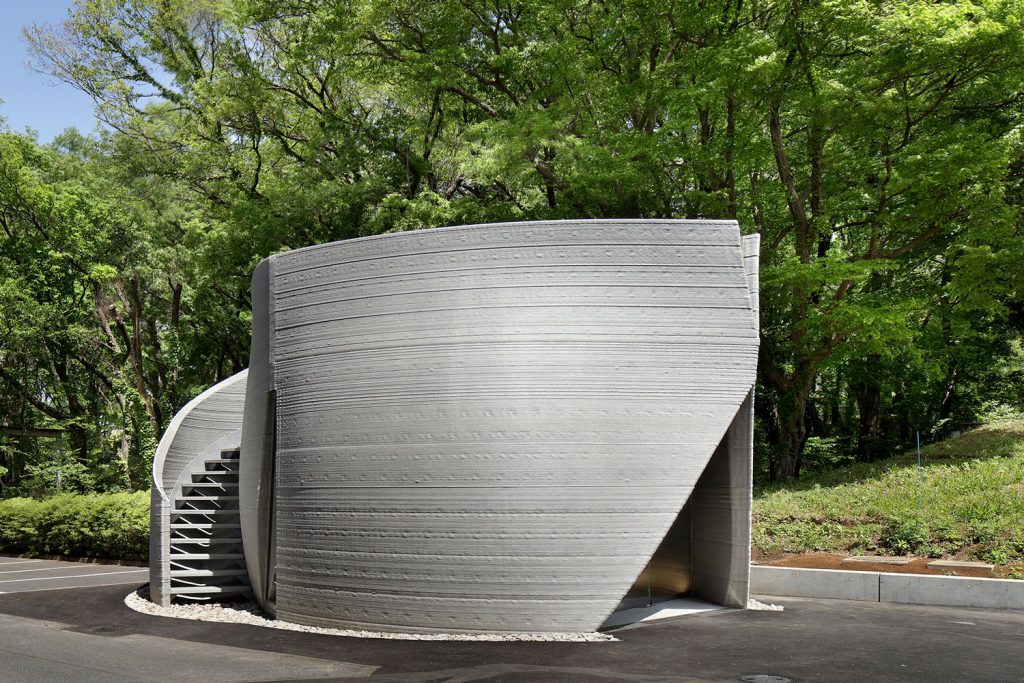
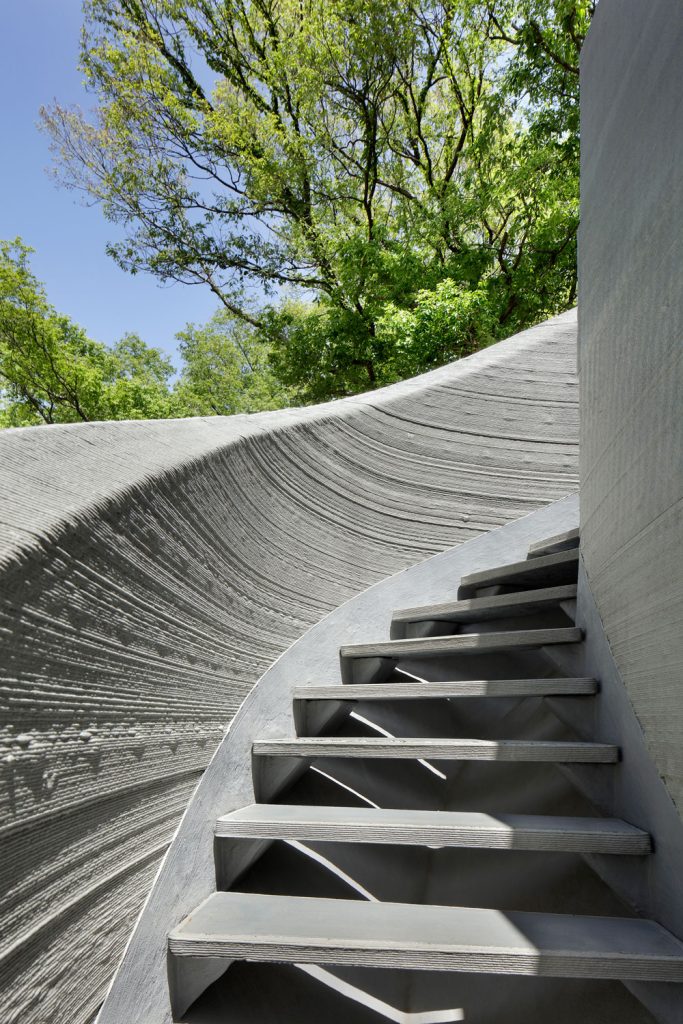
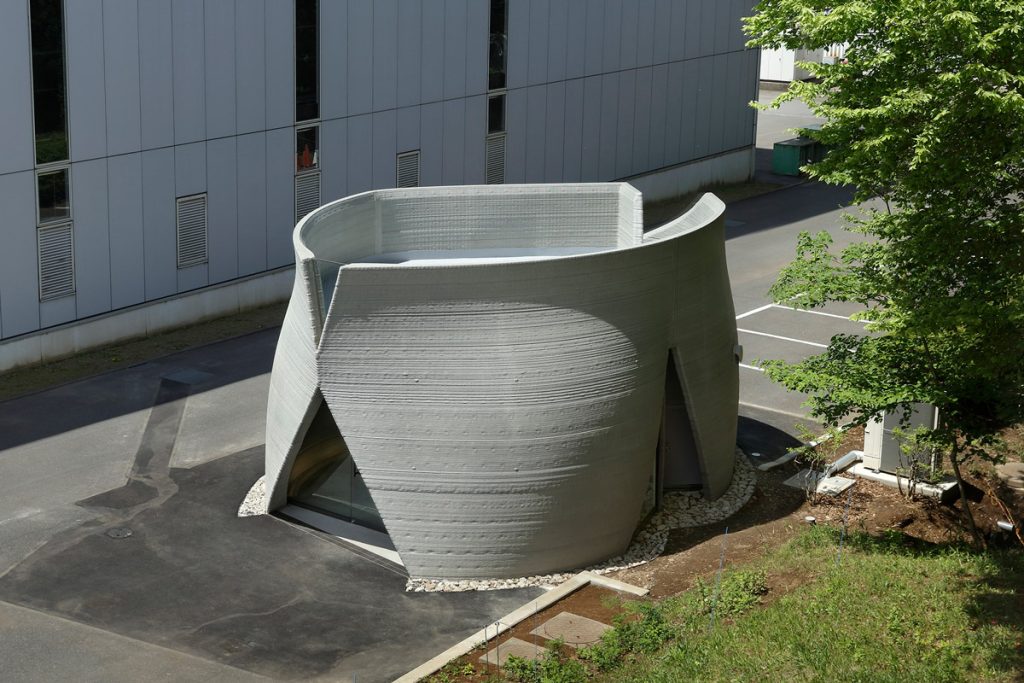
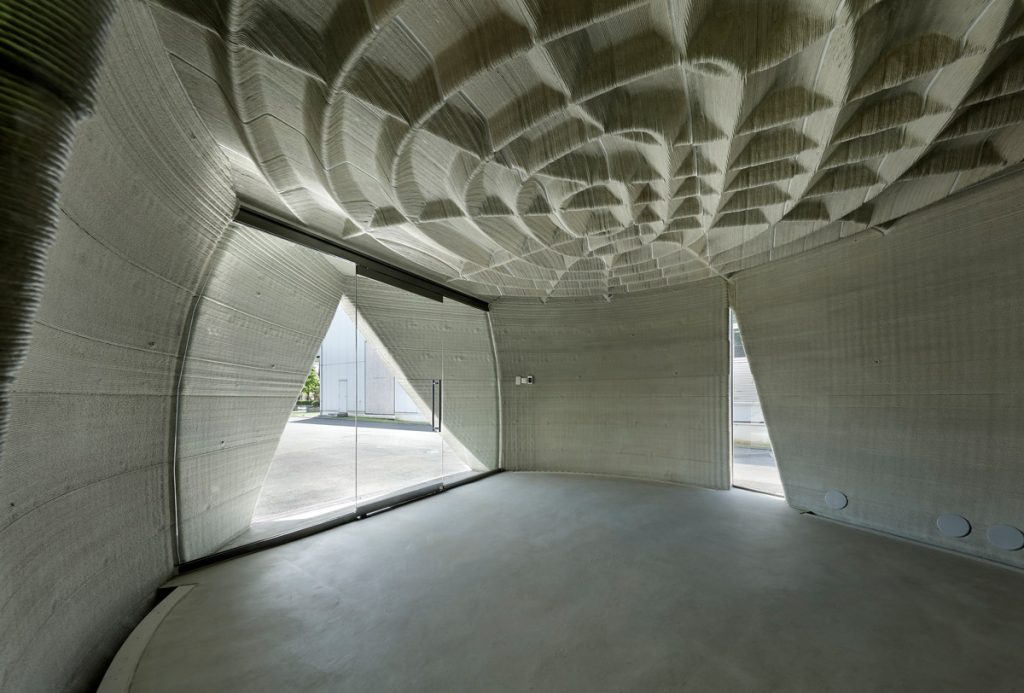
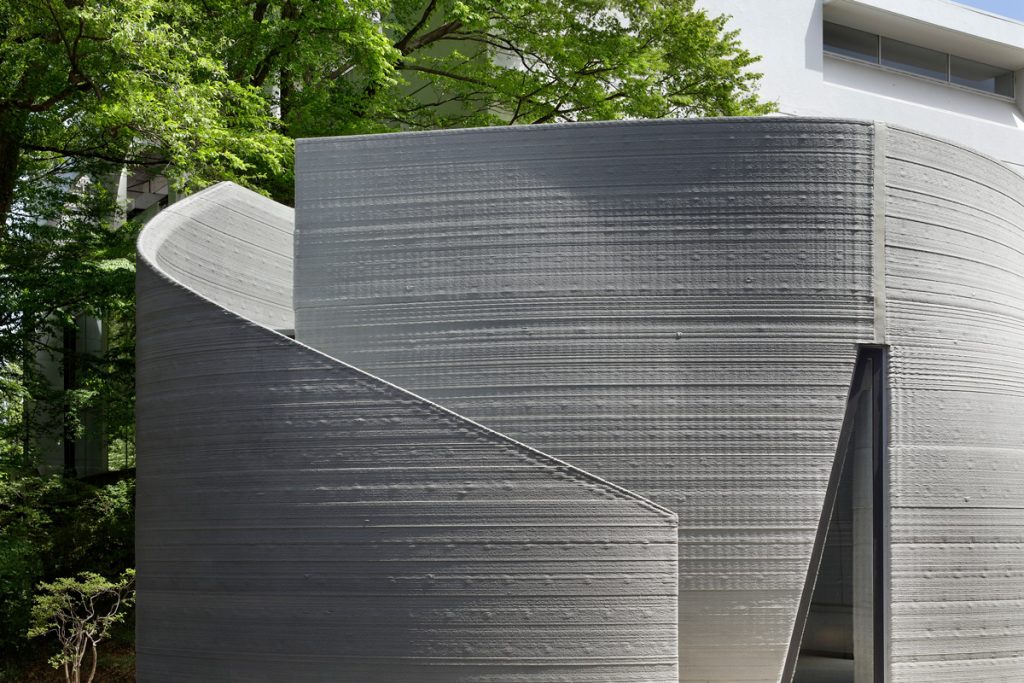
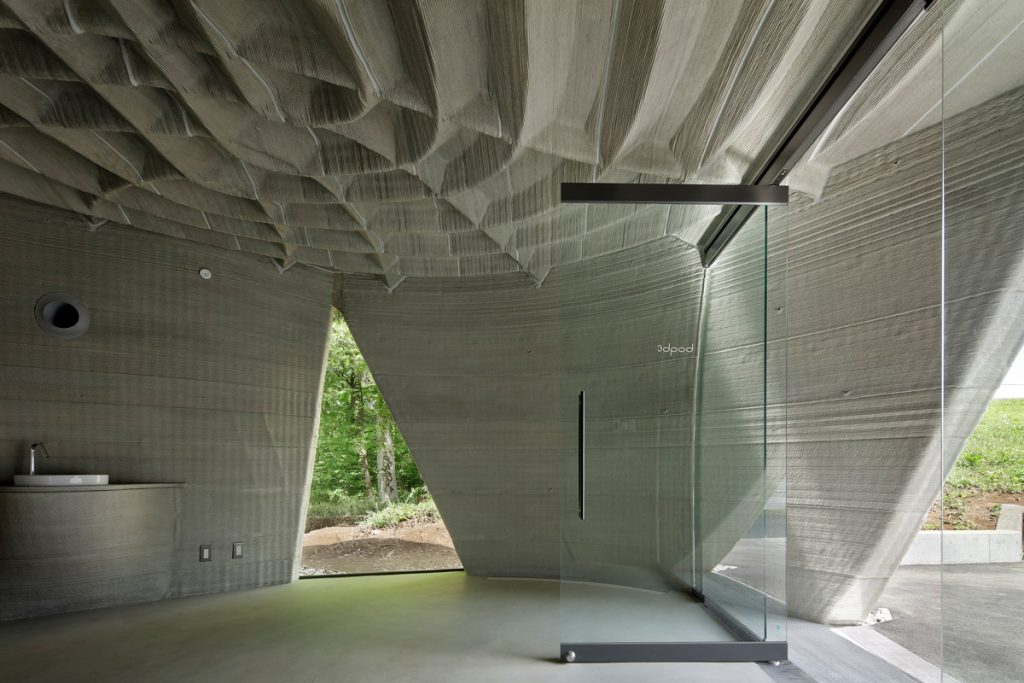
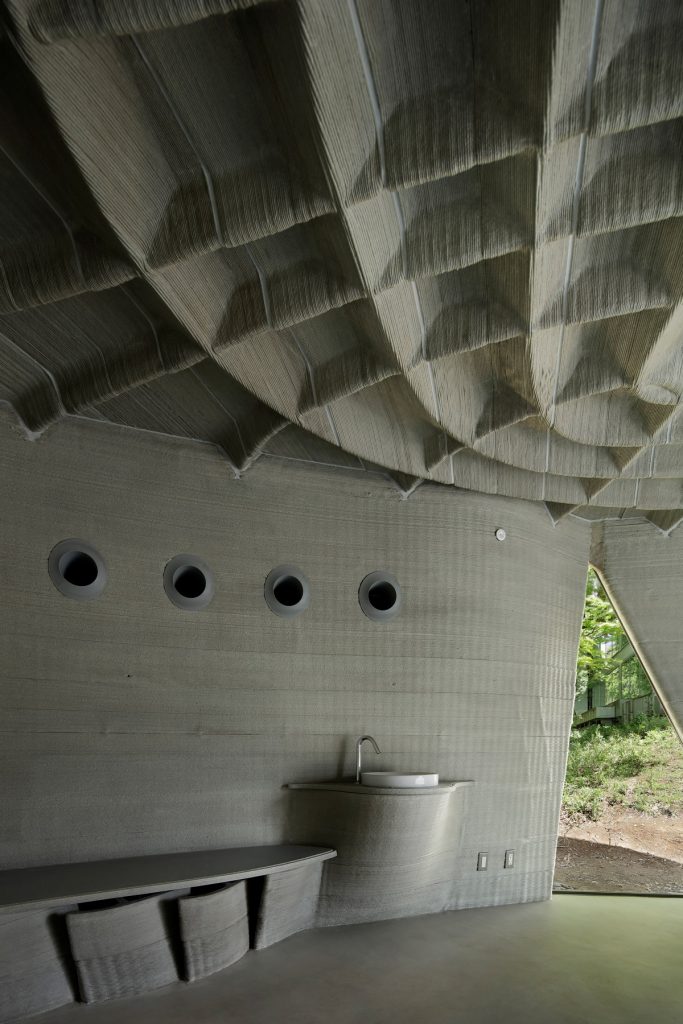
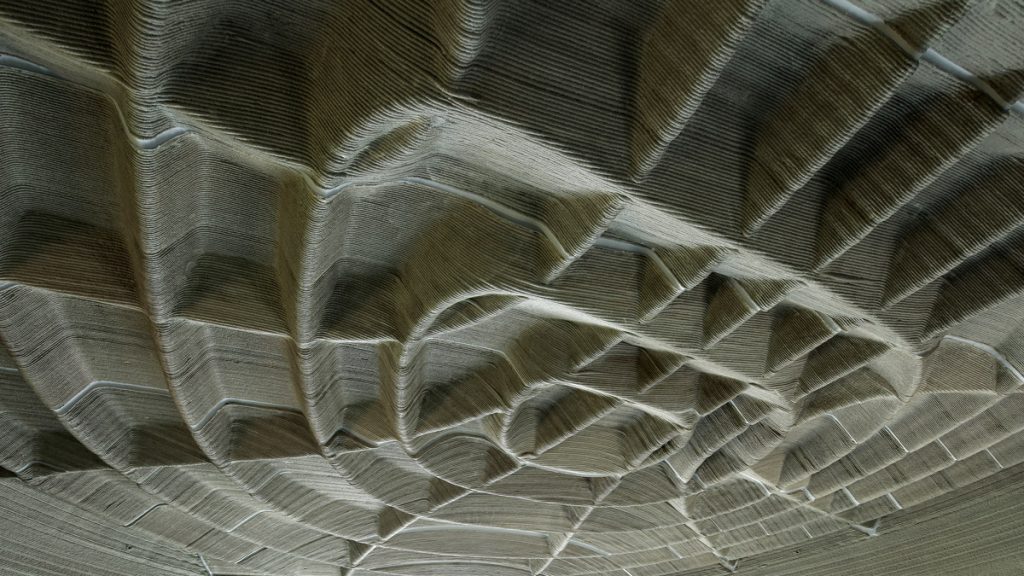
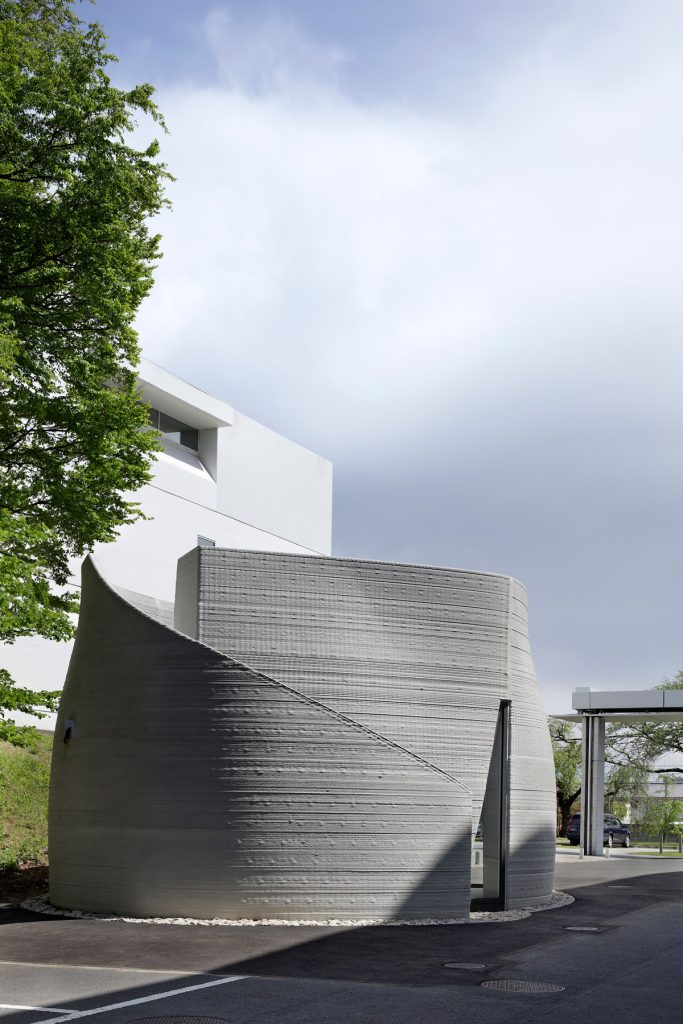
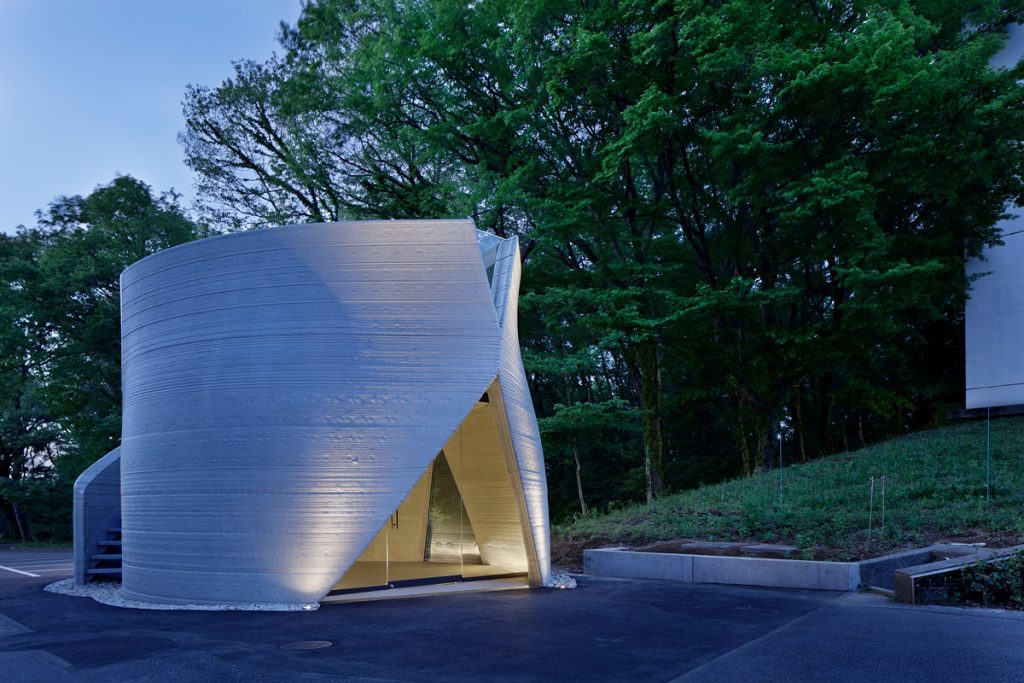
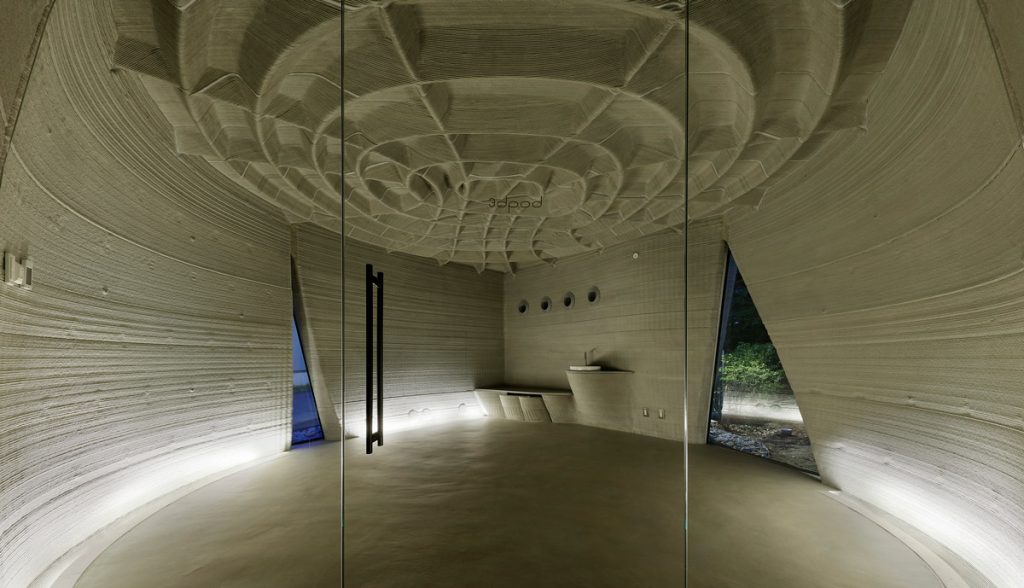